Metals & minerals
Integrating new electrical drive technology into existing machinery is technically complex and usually capital intensive. Our extensive experience is therefore reassuring.
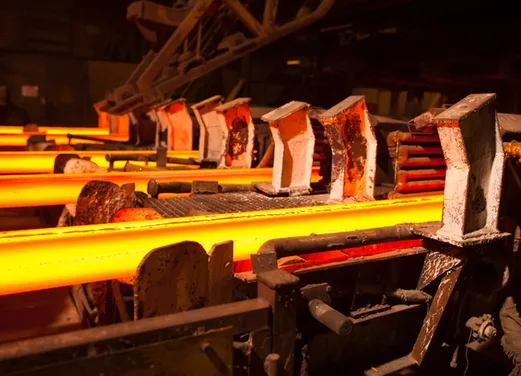
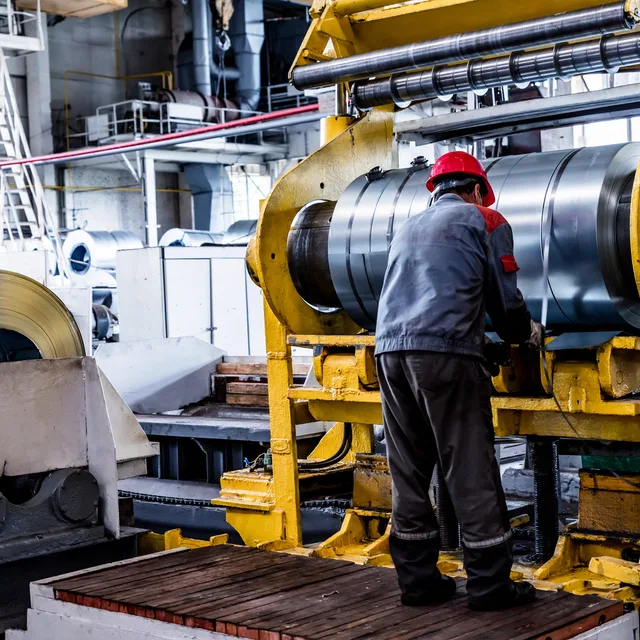
Metals & minerals
Experienced and reliable
Implementing modern electric drive technologies in the metal industry involves numerous technical challenges and significant investments. In this rapidly changing and complex world, it is essential to have a partner with proven experience.
SPIT is exactly that partner. Our broad experience extends from integrating drive systems in hot rolling plants to working on the generator of coke gas plants. We are proud of our involvement in a range of cutting-edge projects and possess the in-depth knowledge essential to the successful completion of such initiatives.
Cold roll reduction work
A cold rolling mill is a machine where metal (such as steel or aluminum) is rolled at ambient temperature to reduce thickness and improve certain mechanical properties.
In the case of this client, the unit consists of five rotating rollers or "stands. Each is equipped with two working rollers driven by direct current motors.
4-High arrangement: each stand has two backup rollers that support the work rolls. These prevent deformation of the work rolls despite the enormous forces during rolling.
Uncoiler & coiler: The process begins with the uncoiler on which coils are placed using an overhead crane. After reduction, the coils are rewound with the coiler.
Roll Gap & Thickness Control: The "roll gap," the space between the working rolls, is adjusted with screw drives. Two thickness measuring devices control the thickness. If the thickness falls outside the desired range, the roll pressure is adjusted accordingly.
Speed & Tension Control: As the thickness of the roll decreases, the speed increases, with speeds up to 900 m/min at the last pass. Tension is controlled by adjusting the speed of the work rolls and is measured between each position with a load cell.
A slitter can optionally be used to remove lateral cut residue.
SPIT was responsible for the entire project. From pre-engineering to software development and panel construction including installation and commissioning. In addition, our automation solution also integrated both profile and emulsion control of this 5-Stand, ensuring accuracy and quality of the final product.
Integration
At SPIT , we combine innovation with adaptive thinking. We see the value in preserving old, reliable systems and strive to integrate them with modern control systems, rather than replacing them costly and time-consuming. An illustration of this is this collaboration with an international customer, where we seamlessly integrated their existing systems with an advanced DCS solution.
What sets us apart is our creative approach combined with a flexible methodology. Every project is unique and deserves a customized solution. Choosing SPIT means choosing a partner that seamlessly weaves technical expertise with adaptive problem-solving capabilities.
Contact
Want to know more?
We would love to hear what your metal/mineral needs are. With our experience and our extensive workshop, we can help you in the way that suits your business.